LDPE 150: Versatile PCR Plastic for Everyday Use
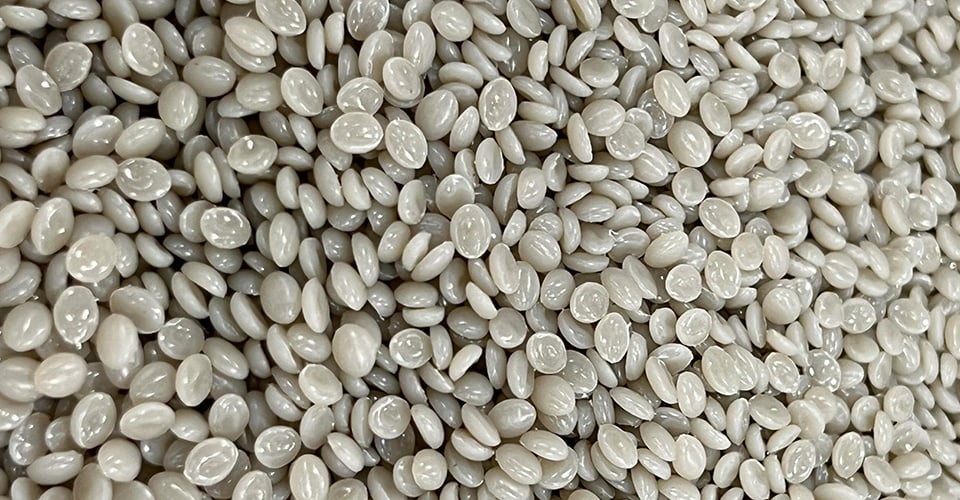
Houston, TX | Oct 1, 2024
Walk through the aisles of any grocery store, and you’ll find low-density polyethylene (LDPE) doing some heavy lifting quietly. It’s the plastic behind everyday items like bubble wrap, tubing and even those six-pack ring carriers clinging to your favorite sodas. It’s flexible, durable and deceptively strong for its softness. At Natura PCR, we’re giving LDPE an upgrade — making it sustainable, circular and surprisingly elegant in its impact.
Introducing LDPE 150: our multi-purpose post-commercial resin that’s far from average. Created from clean, traceable commercial plastic waste and processed into a reliable low density polyethylene film, LDPE 150 offers the usability converters rely on without the environmental compromise.
What Is LDPE Plastic—and How Is It Different from LLDPE Plastic?
LDPE stands for low-density polyethylene, a thermoplastic derived from the polymerization of ethylene gas under high pressure. It’s known for its softness, transparency and excellent resistance to impact and moisture. Structurally, LDPE has a high degree of short and long chain branching, which makes it less dense and more flexible than other polyethylene types.
By comparison, LLDPE (linear low-density polyethylene) has a more linear structure with minimal branching, giving it greater tensile strength and puncture resistance. That makes LLDPE ideal for applications like shrink wrap, stretch film and industrial-strength packaging.
So, where does LDPE fit in? While LLDPE is stronger, LDPE 150 is better suited for everyday uses that don’t require high strength—like dispensing bottles, grocery bags and tubing. LDPE’s softness and processability make it a favorite for converters working with less demanding packaging materials. And because it melts and molds easily, it’s often used for extrusion and molding processes that call for flexibility over rigidity.
Keep Exploring The Difference Between LLDPE And LDPE
Manufacturing LDPE Plastic: The Process
LDPE 150 is created through a carefully controlled recycling process designed to preserve quality and minimize contamination. Unlike traditional virgin plastic, which is made from fossil fuels, Natura PCR’s LDPE PCR plastic is produced from commercial plastic film waste sourced from trusted partners like Walmart, Amazon, Ashley Furniture and Rooms To Go. This targeted, post-commercial feedstock allows us to eliminate many of the unknowns that plague traditional PCR recycling systems and creates the foundation for reliable, high-performance LDPE resin.
Once received, each bale enters our advanced processing system, where state-of-the-art sorting technology removes approximately 90% of contaminants — including foam, cardboard, paper labels and the occasional wood chip. We maximize material recovery (and prioritize plastic resin’s purity) by strategically blending cleaner and slightly more contaminated feedstock to maintain quality while reducing waste. Nothing is wasted unnecessarily. Everything is evaluated for potential.
But our version of circularity doesn’t stop at polyethylene pellets. We partner closely with converters to ensure our LDPE resin meets their evolving needs. If issues arise, our product development and QA teams collaborate directly with clients to fine-tune specifications, optimize performance and keep valuable material in play.
Explore Our Commitment To Circularity
Maintaining Purity: Traceable PCR Plastic Supply
One of the biggest questions we hear is: Where does your PCR plastic come from? And it’s a fair one — because with PCR recycling materials, the quality of the source matters.
Unlike residential recycling, where contamination levels can vary wildly (and let’s be honest… Might include the occasional beer can or... rodent), our commercial feedstock comes from high-volume retailers and furniture distributors with streamlined recycling programs. These overnight stocking teams bale up the film at the back of the store, where it’s picked up by our waste management partner. These packaging materials are clean, consistent and traceable — making our LDPE polyethylene plastic stand out from the crowd.
By maintaining a direct line of communication with each source, we can flag contamination issues and adjust our supply chain in real time. It’s this level of control that allows us to produce high-quality LDPE pellets with consistent performance and a 90% or better purity rate.
Why Use Recycled LDPE Plastic?
Natura PCR’s LDPE PCR resin isn’t trying to beat virgin plastic at its own game, and we’re not pretending it will. Our 100% recycled plastic resin won’t win awards for flawless clarity or extreme strength, but that’s not its purpose. What our LPDE plastic offers is practical, flexible performance for everyday applications — all while playing a vital role in driving the circular economy forward.
Our LDPE resin is made from plastic film waste that’s already served its first purpose. Through our fully traceable and closed-loop supply chain, we reclaim that film, clean it, reprocess it and return it to the market as a high-quality, post-commercial PCR resin. Instead of relying on fossil fuels, we transform waste into worth, helping converters reduce their environmental footprint without sacrificing function.
Because our process is built around accountability at every stage, from source to polyethylene pellet, our clients can be confident in the consistency and integrity of every batch. It’s more than PCR recycling, it’s a regenerative system that protects value, preserves quality and keeps plastic in use and out of landfills.
Explore Our Commitment To Sustainability
Where LDPE Plastic Shines
If there’s one thing our LDPE plastic is known for, it’s versatility. As a multi-use, lightweight resin, it performs reliably across a wide range of everyday applications, including tubing, squeeze bottles, bubble wrap, protective packaging, disposable grocery and garbage bags, containers and dispensing bottles.
One of its most recognizable applications? Six-pack ring carriers. If you’ve noticed a shift from crystal-clear plastic rings to more opaque, slightly speckled ones, you’ve likely seen LDPE 150 in action. Natura PCR supplies this PCR resin to converters like Hi-Cone, who manufacture ring carriers for major beverage brands. So next time you grab a six-pack, take a closer look at the rings, you might just be holding our 100% recycled resin in your hand.
A Flexible Approach to Sampling and Support
We know every companies needs are different, which is why we make the onboarding process as seamless as possible. Our customer journey starts with free PCR resin sampling, not contracts. Whether you’re testing for melt strength, clarity or tensile performance, we’ll work alongside your team to confirm your LDPE resin is the right fit before scaling up.
Our sample program includes complimentary 50-pound PCR resin samples for lab testing, optional gaylord-sized boxes for pilot production and full truckload deliveries for real-world simulation. If anything seems off, our team engages directly with yours to troubleshoot the issue, recommend adjustments, and, if needed, issue a corrective action report.
In the rare event our LDPE resin doesn’t work for your application, we’ll find a more suitable use — because someone, somewhere, can always use a high-quality, everyday recycled plastic resin.
Download LDPE 150 Resin’s Full Specs
A Day in the Life of LDPE Plastic
From the moment our LDPE enters our facility, we handle it with precision. The film is shredded, washed, sorted, and extruded into LDPE pellets—each batch passing quality checks that ensure melt flow, strength, and color consistency are within spec.
Our clients then take those polyethylene pellets and turn them into a wide range of end products. One of the largest converters we supply uses LDPE plastic to make over 2 million grocery bags per day. Another uses it for tubing in non-food packaging. And yet another relies on it for cushioning material like bubble wrap.
It’s the unsung hero behind a thousand product lines — and it’s helping to keep millions of pounds of plastic out of landfills every year.