The Clean Path to Compliance: How We Produce Food Safe Resin For Food and Beverage Packaging Applications
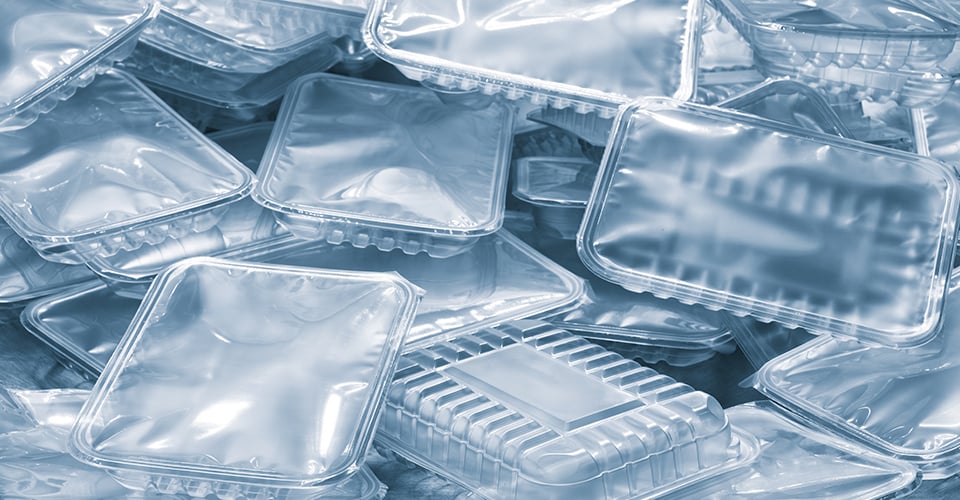
Houston, TX | Oct 1, 2024
Manufacturers and brand owners face increasing pressure to incorporate sustainable materials without compromising product integrity or consumer safety. This challenge is especially critical in food packaging applications, where food packaging materials purity is not just a matter of quality but an obligation.
At Natura PCR, we have developed a rigorous and systematic approach to producing FDA compliant plastic to create food grade packaging that meets the highest purity, performance, and consistency standards. Our linear low-density polyethylene (LLDPE) film represents a breakthrough in post-consumer recycled materials for the food and beverage packaging industry, providing quality and scalability that were previously unavailable.
Unlike LDPE, which is softer and more flexible, LLDPE offers increased strength, puncture resistance, and better load-holding performance. This makes it the preferred material for food packaging bags, custom food packaging and other food and beverage packaging that demand both safety and structural integrity.
While food safe resin solutions aren't new, Natura PCR has redefined what’s possible with our exclusive partnership with a major waste management company, state-of-the-art facilities and rigorous quality controls. Here's how we convert post-consumer materials into food safe resin and empower food packaging suppliers to create eco friendly food and beverage packaging while meeting FDA requirements.
Explore Our Products
Sourcing: Starting with Clean, Traceable Materials
The journey to exceptional food grade packaging begins long before the material reaches our processing facilities. Unlike typical recycled plastic pellets from residential or mixed commercial streams, our food safe resin starts with unprecedented cleanliness and consistency.
We source exclusively from FDA-approved post-commercial film collected from vetted food packaging suppliers and food-only retail stores. Our direct partnerships with major retailers like neighborhood markets, food wholesalers and other selected food distribution centers provide a continuous stream of high-quality, food-contact-approved shrink wrap and flexible plastic food packaging.
This controlled sourcing approach offers several key advantages:
- Material Consistency: We eliminate the variability affecting typical recycling streams by collaborating with established food packaging suppliers and other sources that exclusively manage food and beverage packaging.
- Contamination Control: Our feedstock arrives with significantly lower initial contamination levels — typically around 3-5% compared to the 15-20% found in mixed commercial or residential streams. This ensures alignment with strict FDA compliant plastic standards.
- Complete Traceability: Every bale of material can be traced back to its source, enabling unprecedented quality control throughout the supply chain for food and beverage packaging.
- Continuous Improvement: Our direct relationships with food packaging suppliers create feedback loops that enable rapid corrective actions. If contamination levels increase, we promptly collaborate with the source to identify and resolve issues.
- Scalability: Our waste management partnership provides a consistent and reliable supply of high-quality PCR material, enabling us to increase production to meet rising demand for food grade packaging without sacrificing quality.
This controlled sourcing strategy starkly contrasts with competitors who often depend on mixed commercial or residential streams, where contamination profiles can vary significantly from batch to batch, making consistent food-grade production nearly impossible. Our approach products food safe resin that always meets the stringent requirements for FDA compliant plastic.
Discover Natura PCR’s Commitment to Operational Excellence
Segregation: Ensuring Material Integrity
Once materials arrive at our facility, our segregation protocols preserve the integrity of our food-grade stream from reception to final processing. All incoming food grade packaging materials are:
- Stored in designated areas physically separated from non-food-grade materials.
- Always staged on pallets and stored off the ground to eliminate contamination risks.
- Housed in dedicated and isolated warehouse sections to prevent cross-contamination.
- Sorted by material type and source to maintain batch consistency.
- Assigned unique identification codes for total traceability.
Meticulous segregation continues throughout the facility, employing dedicated handling equipment and production lines. This prevents cross-contamination and ensures our food grade resin consistently meets and exceeds the FDA’s contamination threshold for food and beverage packaging.
Quality Control: Strict Grading and Purity Checks
Before processing begins, each bale undergoes a rigorous quality assessment to ensure it meets our strict standards for food safe resin production. Our multi-layered quality control process includes:
- Visual Inspection: Experienced technicians assess each bale for visible contaminants or non-conforming materials.
- Contamination Grading: Only materials that meet our strict threshold of 3% or lower qualify for food-grade processing. This limit surpasses FDA requirements and reflects our commitment to exceptional quality.
- Material Composition Analysis: Bales are evaluated for uniform PCR plastic composition to ensure reliable processing characteristics.
- Moisture Content Verification: Excess moisture can affect processing quality, so levels are closely monitored.
Any material that does not pass this assessment is immediately downgraded and redirected to our multipurpose LLDPE film production, ensuring that nothing goes to waste while preserving the integrity of our food-safe resin stream.
Explore Our Total Utilization Model
This quality control continues throughout processing using advanced technologies, which include:
- Optical sorting systems that identify and eliminate non-conforming materials
- Multi-stage filtration that progressively removes smaller contaminants
- Continuous monitoring of process parameters to ensure consistent quality.
The outcome is a purity level that consistently exceeds FDA requirements for direct food contact applications.
Devolatilization: Purifying the Resin for Food Contact
Devolatilization is a critical step in producing FDA compliant plastic for food and beverage packaging. This specialized purification technique eliminates volatile organic compounds, residual odors, and potential contaminants that could impact food safety or quality.
Our Post-Crystallization Unit (PCU) subjects the resin to carefully controlled temperature conditions that:
- Force volatile compounds to transition to a gaseous form.
- Extract these gases through a sophisticated vacuum system.
- Remove residual processing aids and other potential contaminants.
- Eliminate odors that could transfer to food products.
- Ensure the final resin meets stringent FDA requirements for chemical migration.
Extrusion and Pelletizing: The Transformation into Resin Pellets
Food-grade pellet production starts with clean, segregated materials on dedicated lines meticulously sanitized between runs. Before processing food grade materials, our equipment undergoes a thorough sanitation process that takes anywhere from 3 to 8 hours, including:
- Complete disassembly and deep cleaning of critical components
- Replacement of cutting blades and other wear parts
- Thorough purging with FDA-approved purging compounds
- Comprehensive cleaning of water tanks and cooling systems
- Inspection and verification of cleaning effectiveness
- Reassembly under controlled conditions
- Line startup with material testing to confirm quality
We maintain high temperature profiles throughout extrusion, eliminating bacteria and other microbiological contaminants. These temperature-controlled conditions provide an extra safety barrier beyond standard recycling processes.
The material goes through several filtration stages during extrusion, utilizing progressively finer mesh screens that eliminate any remaining particulate contamination and ensure consistent performance throughout the production run.
Our pelletizing systems produce uniform polyethylene pellets with consistent size, shape, and processing characteristics — critical factors for downstream converting operations. Each batch undergoes comprehensive testing to ensure our food safe resin always meets the following specifications:
- Melt flow rate (typically 0.6–1.5 g/10 min)
- Density (0.917–0.920 g/cm³)
- Tensile strength (14–22 MPa)
- Elongation properties (300–600%)
- Color consistency and clarity
Only material meeting all specifications advances to storage and shipping as certified food-grade resin.
Explore The Full Specifications
Storage: Keeping the Resin Safe and Compliant
Maintaining the integrity of our FDA compliant plastic doesn't stop at processing—it extends all the way through storage and shipping. Our certified food-grade resin, made from high-quality PCR plastic, is stored in dedicated silos specifically engineered for food and beverage packaging. These silos are physically separated from all other materials and exclusively reserved for LLDPE food-grade resin — even when not in use — to prevent contamination and uphold the strictest hygiene standards.
Whether destined for small food packaging, custom food packaging, or larger-scale food packaging containers, our finished PCR resin is handled with the same level of care throughout every stage. We use only FDA-compliant packaging materials for shipping both food grade packaging and general-purpose products. This eliminates the risk of cross-contamination and ensures that every batch of resin — whether LDPE or LLDPE plastic — meets the highest standards of quality and compliance.
Our storage and logistics practices are designed to support customers across the full spectrum of plastic food packaging needs, from eco-friendly food packaging to flexible food packaging bags. Backed by a commitment to safety, consistency and performance, Natura PCR delivers dependable solutions for converters, food packaging suppliers and manufacturers seeking trusted food packaging materials made from premium PCR material.
Compliance and Certification: Meeting FDA and Industry Standards
Regulatory compliance is integrated into every step of Natura PCR's process. Our food-grade LLDPE resin is manufactured per FDA regulations for food-contact materials, specifically 21 CFR 177.1520, which pertains to olefin polymers. This FDA compliant plastic is engineered for use across a wide range of food and beverage packaging applications, delivering both safety and sustainability.
Our robust compliance program includes:
- Comprehensive documentation of material sources and processing conditions
- Regular third-party testing to verify compliance with chemical migration limits
- Batch-specific certificates of analysis documenting key quality parameters
- Ongoing employee training on food-contact safety standards
- Scheduled audits of all facilities and processes
Learn More About Formulating Your Custom Food Packaging Resin
Custom Food Packaging Solutions
We understand that every customer has unique purity and performance requirements — especially when it comes to food packaging materials. From creating custom formulas using high-quality LLDPE plastic to refining blends that align with your specifications, we provide hands-on collaboration through sample testing, scale trials, and ongoing optimization. Whether you're producing food packaging bags, food packaging containers, or launching eco-friendly food packaging, our FDA-compliant, high-purity PCR resin ensures you meet regulatory standards while maintaining peak product performance.
By following a proven step-by-step support model — including customization, delivery, and ongoing refinement — we help food packaging suppliers and manufacturers bring safer, smarter and more sustainable solutions to market.
Learn More About Formulating Your Custom Food Packaging Resin